The choice between sublimation or screen printing techniques for apparel depends on various factors such as design complexity, quantity, fabric type, and desired outcome. Both techniques have their advantages and considerations.
Screen printing is preferable for simple designs and offers excellent durability, versatility, and compatibility with various fabrics. On the other hand, sublimation excels in complex designs, vibrant colors, and photographic prints, but is limited to polyester-based light-colored fabrics. Consider your specific requirements and budget to determine which printing method suits your needs best.
So buckle up and get ready for a titanic battle as we examine the advantages, disadvantages, and all the minute nuances that will determine which technology ultimately succeeds in the field of garment printing. “The Ultimate Print Face-Off: Screen Print vs. Sublimation in Apparel” is coming up, so be ready!
Sublimation Printing: What It Is and How It Works
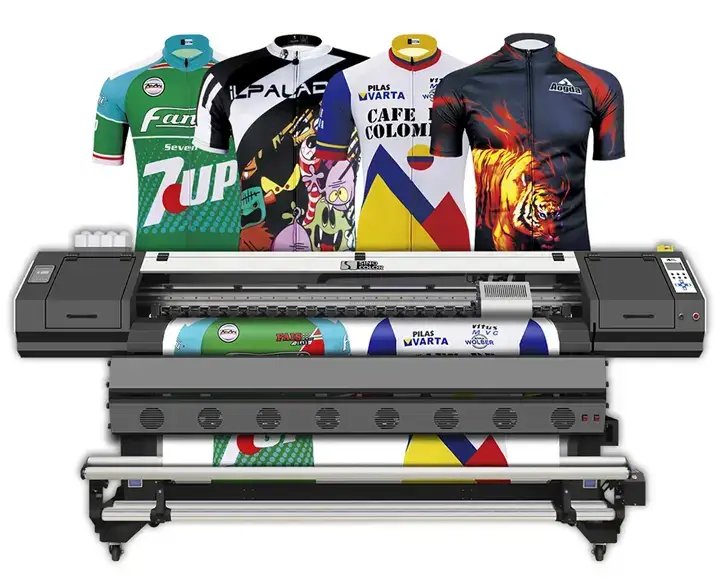
What Is Sublimation Printing?
Sublimation printing is a digital printing method that involves transferring dye onto a substrate (typically polyester fabric fibers or items with a polymer coating) using heat and pressure. Unlike traditional printing techniques and other dye transfer techniques, sublimation printing is a digital printing technique that uses dye in a gas state instead of a liquid state. It involves the conversion of a solid dye into a gas. This process allows the dye to penetrate the fibers of the fabric or the coating of the item, resulting in vibrant, full-color, and long-lasting prints.
Sublimation printing is widely used for custom apparel, sportswear, promotional items, flags, banners, and various other polyester-based products. Its ability to reproduce vibrant, detailed, and long-lasting designs makes it a popular choice in the textile printing industry.
How does sublimation printing work?
Here’s how the sublimation printing process works:
Design Preparation: The first step is to create or prepare a digital design using graphic design software.
Printing onto Transfer Paper: The prepared design is then printed onto a special sublimation transfer paper using dedicated sublimation ink.
Transfer Process: The printed transfer paper is carefully placed face-down onto the surface of the substrate, ensuring proper alignment.
Heat and Pressure Application: The transfer paper and substrate are placed together into a heat press machine. The heat transfer machine applies heat and pressure, causing the sublimation inks on the transfer paper to convert directly from a solid to a gas state.
Sublimation: The heat and pressure applied in the heat press cause the sublimation ink on the transfer paper to convert directly into a gas without passing through a liquid state. This gas permeates the polyester fibers or polymer coating of the item.
Ink Solidification: As the heat press is removed and the fabric or item cools down, the sublimation ink gas solidifies, becoming a permanent part of the fabric or coating. The result is a vivid, high-quality, and durable image that won’t crack, peel, or fade easily.
Final Inspection: After the substrate has cooled, remove the transfer paper. Inspect the printed design for any imperfections or issues. Sublimation prints are generally dry and ready to use immediately after cooling.
What can you do with sublimation printing?
Sublimation printing offers a wide range of possibilities and is commonly used in various industries for different applications. Here are some examples of what you can do with sublimation printing:
Custom Apparel: Sublimation printing is frequently used for creating custom clothing items such as t-shirts, jerseys, hoodies, leggings, and activewear. It allows for full-color, vibrant designs with intricate details and patterns.
Sportswear and Team Uniforms: Sublimation is popular in the sports industry as it enables the production of personalized jerseys, shorts, socks, and other sportswear items. Teams can have unique designs, logos, and player names or numbers.
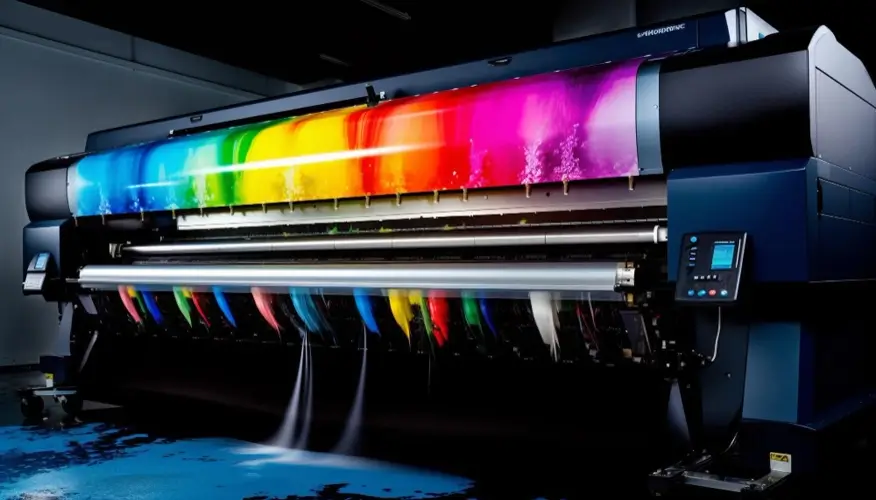
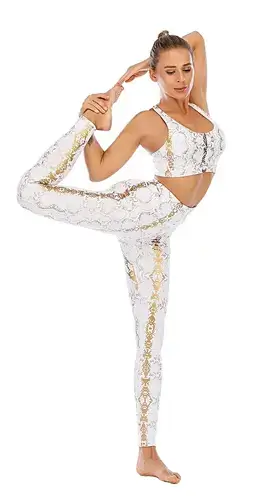
Promotional Products: Sublimation printing is utilized for producing promotional items like mugs, keychains, mousepads, coasters, and phone cases. These items can feature custom designs, logos, or branding, making them effective marketing tools.
Home Decor: Sublimation is used for creating personalized home decor products such as throw pillows, blankets, towels, wall art, and ceramic tiles. It allows for detailed and vibrant prints that can enhance the aesthetic appeal of living spaces.
Signs and Banners: Sublimation is utilized for producing high-quality signs, banners, and flags. The process allows for full-color printing on polyester-based materials, resulting in eye-catching displays for events, trade shows, and businesses.
Personalized Gifts: Sublimation printing enables the creation of unique and personalized gifts for special occasions. Items like photo frames, mugs, puzzles, and custom clothing can be customized with personal photos, messages, or artwork.
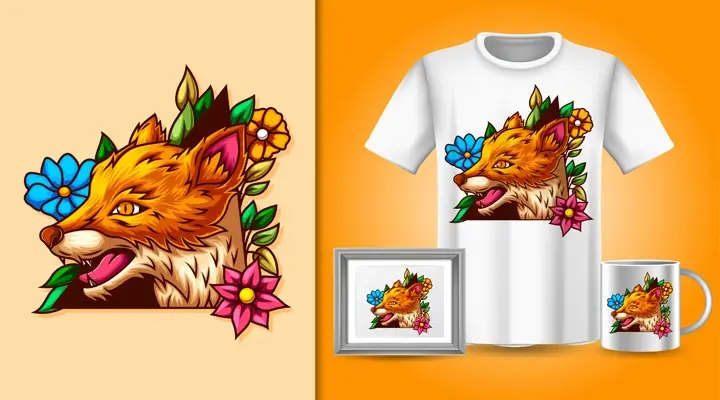
Fashion Accessories: Sublimation is utilized for designing fashion accessories such as scarves, headbands, bags, and hats. It offers the flexibility to create intricate and colorful patterns that complement various outfits.
Customized Office Supplies: Sublimation printing can be used to personalize office supplies like mousepads, desk organizers, notebooks, and pens. This allows for branding or customization with unique designs or logos.
The Benefits of Sublimation Printing
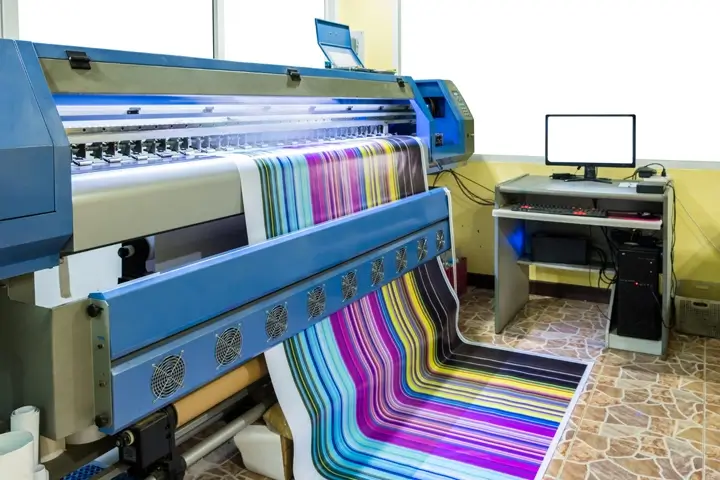
Sublimation printing offers several benefits that make it a preferred choice for many applications. Here are some key advantages of sublimation printing:
Vibrant and High-Quality Prints: Sublimation printing allows for the reproduction of vibrant, full-color designs with excellent color accuracy and clarity. It can capture intricate details, gradients, and photographic images, resulting in visually appealing prints with fantastic print quality.
Durability and Longevity: Sublimation prints have exceptional durability. The dye molecules in sublimation ink bond with the polyester fibers or polymer coating of the substrate at a molecular level. This results in prints that are resistant to fading, cracking, or peeling, even with repeated washings or extended use.
Full-Color and Complex Designs: Unlike other printing methods, sublimation printing does not have limitations on the number of colors used in a design. It can reproduce unlimited colors, gradients, and shading, allowing for intricate and complex designs with smooth color transitions.
No Color Limitation or Color Separation Costs: Sublimation printing does not incur additional costs for multiple colors. The same heat transfer paper can be used to print full-color designs without the need for color separations or screens, making it cost-effective for designs with many colors.
Versatility on Different Substrates: Sublimation printing can be done on a wide range of polyester-based materials, including fabrics, apparel, and items with a polymer coating. This versatility allows for customization across various products such as clothing, accessories, home decor, promotional items, and more.
Soft and Breathable Prints: Sublimation prints do not add any additional layers or textures to the fabric or substrate. The ink becomes a part of the printed material itself, resulting in a soft and breathable finish that does not affect the feel or comfort of the product.
Quick Turnaround Time: Sublimation printing offers fast production turnaround times, especially for small to medium-sized orders. Once the design is prepared and the printing equipment is set up, the actual printing process is relatively quick, allowing for efficient production.
Environmentally Friendly: Sublimation printing is considered environmentally friendly compared to other traditional screen printing inks and methods. The process produces minimal waste, as there are no screens or plates to dispose of, and the sublimation printer inks are non-toxic and safe for the environment.
Sublimation Drawbacks
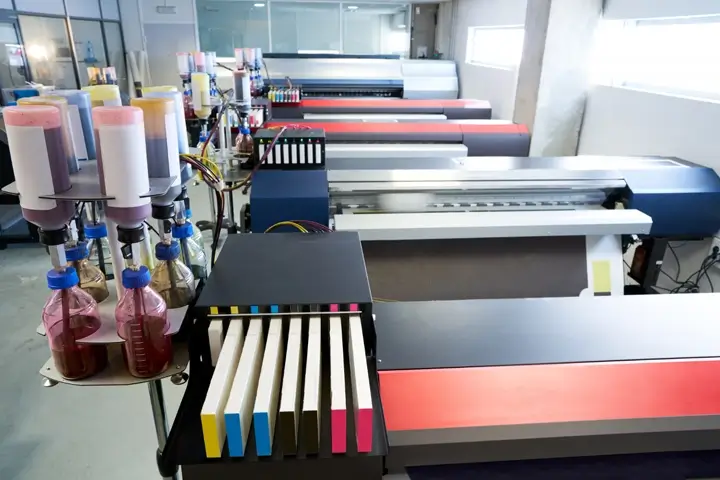
While sublimation printing offers many advantages, there are also some drawbacks and considerations to keep in mind:
Limited Substrate Compatibility: Sublimation printing is limited to polyester-based materials, synthetic fabrics, or items with a polymer coating. It does not work effectively on natural fibers like cotton or non-polymer-coated surfaces. This limits the range of substrates that can be used for sublimation printing.
Light-Colored or White Substrate Requirement: Sublimation printing works best on light-colored or white substrates. Since the sublimation process relies on the dye bonding with the substrate, darker or colored substrates can affect the color accuracy and vibrancy of the prints.
Higher Initial Investment: Sublimation printing requires specialized equipment such as sublimation printers, heat press machines, and sublimation inks. The initial investment for these tools can be higher compared to traditional printing methods, making it a consideration for small-scale operations.
Limited Design Placement Options: Sublimation printing is typically limited to flat surfaces due to the nature of the heat press machine. It can be challenging to achieve precise design placement on contoured or uneven surfaces, which may impact certain product applications.
Not Suitable for 100% Cotton: Sublimation ink does not bond effectively with natural fibers like cotton. As a result, sublimation printing is not suitable for 100% cotton fabrics. However, there are sublimation transfer papers available for cotton blends that allow for a distressed or vintage look.
Limited Color Control on Dark Fabrics: Sublimation printing does not provide the same level of color vibrancy and control on dark fabrics as it does on light-colored or white fabrics. The ink is transparent, so the color of the fabric may affect the appearance of the print.
Longer Production Time for Large Orders: While sublimation printing is efficient for small to medium-sized orders, the process can take longer for large-scale production. Printing each item individually using a heat press can be time-consuming compared to other high-volume printing methods.
Heat Press Limitations: Sublimation printing requires the use of a heat press machine, which may have limitations on the size and thickness of the substrates that can be processed. This can impact the range of products that can be printed using a sublimation printer.
Screen printing: What It Is and How It Works
What Is Screen Printing?
Screen printing, also known as silk screen printing or screening, is a popular printing technique that involves transferring ink onto a substrate using a mesh screen. It is a versatile and widely used method for printing designs on various materials, including textiles, paper, plastics, glass, and metals.
Screen printing is known for its ability to produce vibrant and long-lasting prints, especially on fabrics and other porous materials. It is widely used for creating custom apparel, posters, signage, promotional products, and more.
How does screen printing work?

Here’s an overview of the screen printing process:
Design Preparation: Create a digital image using a graphic designing software or obtain a design that will be printed. The design is typically prepared digitally or hand-drawn on a transparent film or stencil.
Screen Preparation: A screen is constructed by stretching a fine mesh, traditionally made of silk (hence the name “silk screening”), tightly onto a frame. The screen is then coated with a light-sensitive emulsion or a stencil film.
Image Exposure: The design is transferred onto the screen through a process called exposure. In the case of emulsion, a film positive of the design is placed on top of the screen, and both are exposed to UV light. The light hardens the emulsion, except in the areas blocked by the design, creating a stencil.
Screen Setup: The prepared screen is mounted onto a screen printing press, which holds the screen securely in place. The substrate (e.g., fabric, paper) to be printed is positioned on the printing surface below the screen.
Ink Application: A specific color of ink is applied to the top edge of the detailed screen print stencil. A squeegee is then used to pull the ink across the screen, forcing it through the open areas of the stencil and onto the substrate below. The mesh openings allow the ink to pass through onto the substrate while blocking it in areas covered by the stencil.
Printing Process: The squeegee is moved firmly and evenly across the screen, applying pressure to ensure proper ink transfer. This process may need to be repeated for each color in the design. Each color requires a separate screen and printing pass, allowing for layering and mixing of colors to achieve the desired result.
Drying and Curing: Once the design is printed, the substrate is typically dried or cured to set the ink permanently. This may involve air drying, heat curing, or using specialized drying equipment, depending on the type of ink and substrate used.
What can you do with screen printing?
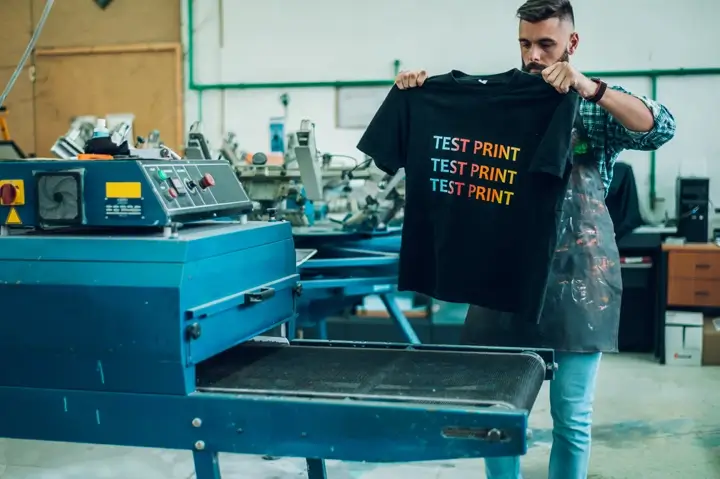
Screen printing is a versatile printing technique that can be used for a wide range of applications. Here are some common uses of screen printing:
Apparel Printing: Screen printing is widely used for custom apparel, including t-shirts, hoodies, sweatshirts, jerseys, and other garments. It allows for vibrant, long-lasting prints on various fabric types, making it popular for creating personalized clothing and merchandise.
Promotional Products: Screen printing is utilized for producing promotional items such as tote bags, caps, pens, keychains, and drinkware. It can efficiently print logos, slogans, and brand information on different surfaces, making them effective marketing tools.
Posters and Art Prints: Screen printing is often used to create posters, art prints, and limited edition prints. The screen printing technique allows for bold colors, sharp lines, and a tactile quality that enhances the visual impact of the artwork.
Signage and Banners: Screen printing can produce durable and weather-resistant signage and banners. It is commonly used for outdoor signage, trade show displays, event banners, and other large-format prints that require longevity and color vibrancy.
Decals and Stickers: Screen printing is ideal for producing high-quality decals and stickers. It can print intricate designs and vibrant colors on vinyl or other suitable materials, allowing for customization of product labels, vehicle decals, laptop stickers, and more.
Textile Printing: Screen printing is used for textile printing beyond apparel, such as fabric panels for home decor, tablecloths, curtains, and linens. It enables the application of designs to textiles for interior design and commercial applications.
Industrial Applications: Screen printing is utilized in various industrial applications, including printed circuit boards, membrane switches, product packaging, and electronic displays. It allows for precise and durable printing on a range of substrates.
Specialty Applications: Screen printing can be applied to unconventional materials such as wood, glass, ceramics, and metals. This opens up opportunities for customizing products like promotional mugs, glassware, signage, and unique artwork.
Benefits of Screen Printing Process
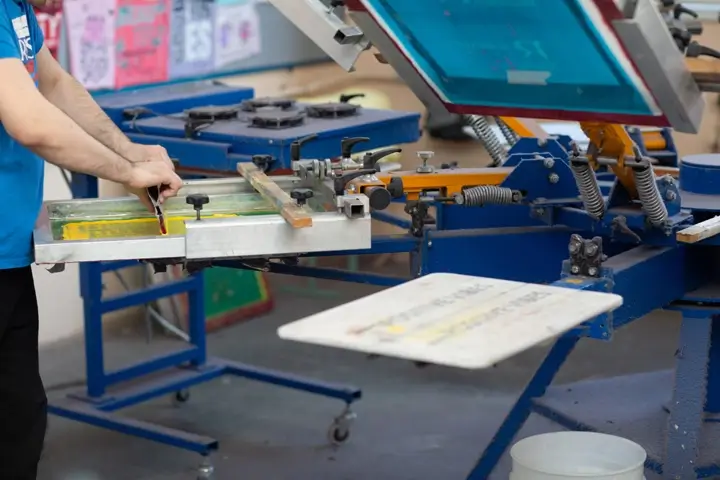
Screen printing offers several benefits that contribute to its popularity and widespread use. Here are some key advantages of screen printing:
Durability: Screen printing produces highly durable prints that can withstand repeated wear and washing.
Vibrant and Opaque Colors: Screen printing allows for the application of thick layers of ink, resulting in vibrant and opaque colors that stand out on various substrates. This makes it ideal for printing on dark-colored or textured materials where other printing methods may not produce the same level of color saturation.
Versatility of Substrates: Screen printing can be used on a wide range of substrates, including fabrics (cotton, polyester, blends), paper, plastics, glass, metals, and more. This versatility makes it suitable for printing on apparel, promotional products, signage, industrial materials, and various other surfaces.
Cost-Effective for Large Quantities: Screen printing becomes more cost-effective as the quantity of prints increases. Once the screens are prepared, the actual printing process is relatively quick, making it efficient for high-volume orders. This makes screen printing a preferred choice for bulk production and large quantities.
Customization and Color Matching: Screen printing allows for precise customization and color matching. Pantone colors can be accurately reproduced, ensuring consistency across multiple prints. It also offers flexibility in terms of layering colors and creating unique effects with specialty inks like metallic or glow-in-the-dark.
High Print Quality and Detail: Screen printing can produce high-quality prints with sharp lines, fine details, and consistent results. The stenciled mesh screen allows for precise control over the ink application, resulting in accurate and intricate designs.
Longevity and Resistance to Fading: The thick ink layers in screen printing create a strong bond with the substrate, making the prints resistant to fading, cracking, and peeling. This makes screen-printed designs durable and suitable for long-term use in various applications.
Ability to Print on Uneven Surfaces: Screen printing can adapt to uneven or irregular surfaces, such as curved objects or textured materials. The flexibility of the mesh that screen print transfers allows it to conform to different shapes, ensuring proper ink transfer and coverage.
Screen Printing Drawbacks
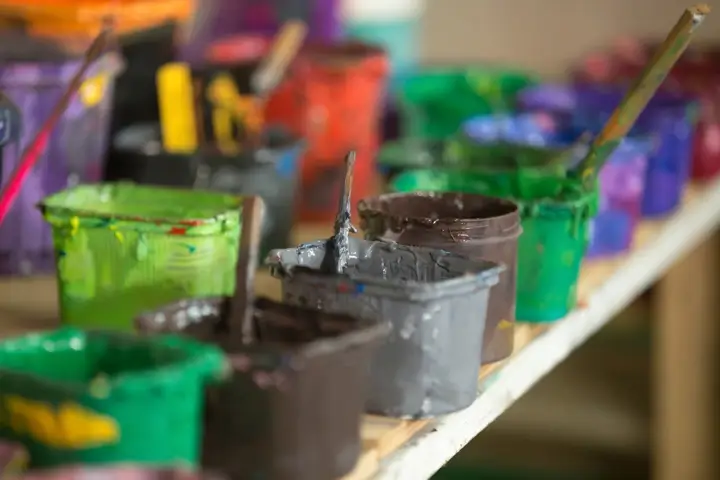
While screen printing offers many advantages, there are also some drawbacks and considerations to keep in mind.
Setup Time and Cost: Screen printing requires the creation of screens for each color in the design, which involves a setup process. Therefore, screen printing may not be cost-effective for small quantities or designs with multiple colors.
Limited Color Variations: Each color in a design requires a separate screen and printing pass, which can limit the number of colors that can be used in a print. Achieving complex color gradients or photorealistic images may be challenging with screen printing.
Detail Limitations: While screen printing can produce high-quality prints, it may not be suitable for extremely fine details or intricate designs. The mesh size and ink viscosity can impact the level of detail that can be achieved. Small text or intricate lines may not come out as sharp or clear as desired.
Limited Substrate Compatibility: While screen printing can be used on various substrates, it may not be suitable for all materials. It works best on porous surfaces such as fabrics, paper, and wood. Non-porous surfaces like glass, metal, or plastics may require additional pre-treatments or specialized inks for optimal adhesion.
High Ink Consumption: Screen printing often requires a significant amount of ink, especially when printing large areas or solid colors. This can increase costs and result in a heavier feel on garments compared to other printing methods.
Longer Production Time for Multicolor Designs: Printing multicolor designs with screen printing can be time-consuming. Each color requires separate setup, printing, and drying time. This can extend the overall production time, especially for complex designs with multiple colors.
Limited Adjustability: Once the screens are prepared, it can be challenging to make changes to the design or colors. Modifications may require creating new screens and repeating the setup process, resulting in additional time and cost.
Environmental Considerations: Screen printing involves the use of inks and cleaning chemicals that can be harmful to the environment if not properly managed. Care must be taken to dispose of waste ink and chemicals responsibly and use eco-friendly options whenever possible.
Sublimation vs. Screen printing: What Are The Differences?
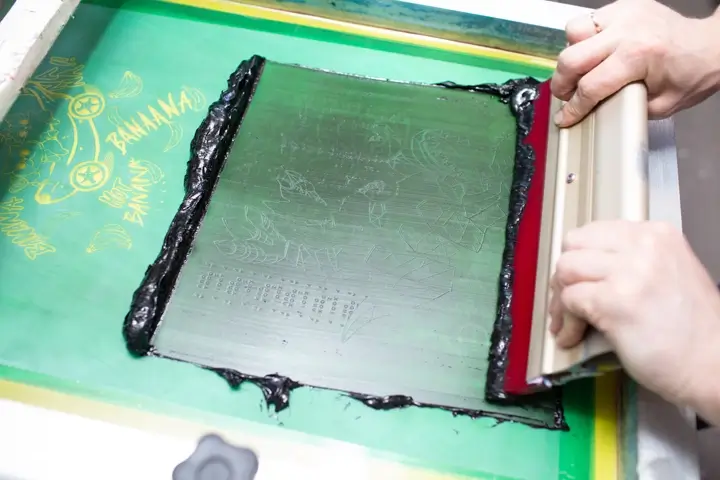
Sublimation printing and screen printing are two distinct printing methods, each with its own characteristics and applications.
Printing Technique
Sublimation printing involves the direct transfer of ink from a solid to a gas state, which then permeates the fibers of the substrate. In contrast, screen printing applies ink onto the surface of the substrate using a mesh screen and a squeegee.
Print Quality
Sublimation printing offers excellent print quality, especially for reproducing intricate details, gradients, and photorealistic images. Screen printing can also produce high-quality prints with vibrant colors and sharp lines. However, it may have limitations when it comes to reproducing fine details or complex gradients, especially compared to sublimation printing.
Print Longevity
Sublimation prints are highly durable and long-lasting. The ink is embedded within the fabric, making it resistant to fading, cracking, or peeling. With proper care, sublimated prints can maintain their vibrancy even after multiple washes. Screen printing also offers good durability, but the prints sit on top of the fabric and may show signs of wear over time.
Design Flexibility
Sublimation printing offers excellent design flexibility, allowing for all-over prints and edge-to-edge coverage on garments. It can seamlessly cover curved or irregular surfaces. Screen printing allows for precise placement of designs but may have limitations when it comes to large or all-over prints.
Color Vibrancy and Details
Sublimation printing allows for unlimited colors and the reproduction of complex color gradients. It can produce vibrant, full-color prints with a high level of color accuracy. Screen printing is limited by the number of screens used in the printing process, making it more suitable for designs with a limited color palette.
Fabrics and Materials
Sublimation printing works best on polyester or polyester-blend fabrics. The ink chemically bonds with the polyester fibers, resulting in vibrant, durable, and wash-resistant prints. Screen printing works best on a wide range of fabrics, including cotton, polyester, blends, and other materials.
Eco-friendliness
In terms of eco-friendliness, sublimation printing has an advantage over traditional screen printing due to the absence of harmful chemicals in the inks and the minimal waste generation during the printing process. However, it’s important to note that screen printing has made advancements in recent years with the introduction of eco-friendly inks and sustainable practices.
Cost Efficiency
Sublimation printing tends to be more cost-effective for small quantities or designs with a high number of colors. The cost per print remains consistent regardless of the number of colors used. Screen printing becomes more cost-effective for large quantities, as the setup costs can be spread out over a higher volume.
Print Feel and Breathability
Sublimation printing produces prints that are integrated into the fabric fibers, resulting in a soft and breathable finish. The print does not add any additional layers or textures to the fabric. In contrast, screen printing adds a layer of ink on top of the fabric, which may have a heavier feel and affect breathability.
Production Time
Sublimation printing typically requires less production time as it eliminates the need for multiple setup steps and color registration. Screen printing, especially for complex designs with multiple colors, may require more time for setup, printing, and drying between each color layer.
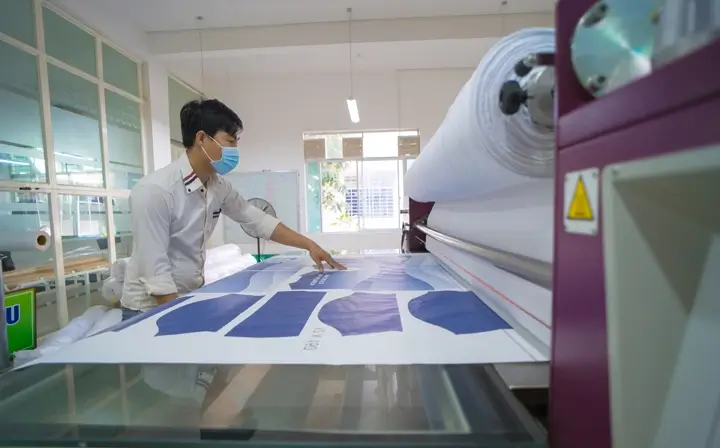
Final Words
In conclusion, both sublimation printing and screen printing have their unique characteristics, benefits, and considerations. Here’s a summary of the key points for each method:
Sublimation Printing:
- Ideal for polyester or polyester-blend fabrics.
- Offers vibrant, full-color prints with excellent detail and color accuracy.
- Provides a soft and breathable finish with durability and wash resistance.
- Allows for customization, all-over prints, and edge-to-edge coverage.
- Works well for small quantities or designs with multiple colors.
- Requires specific equipment and materials for the sublimation process.
- More eco-friendly with minimal waste and water-based inks.
Screen Printing:
- Suitable for a wide range of substrates, including fabrics, paper, plastics, and more.
- Offers vibrant colors and durability, particularly on cotton and cotton-blend fabrics.
- Cost-effective for large quantities and designs with limited colors.
- Allows for precise customization and placement of designs.
- Can achieve high-quality prints with sharp lines and solid colors.
- Setup time and cost may be higher, especially for small quantities.
- Eco-friendliness depends on ink choices, waste management, and energy consumption.
Ultimately, the choice between using sublimation print and screen print depends on various factors such as the fabric or substrate, design complexity, desired color vibrancy, production quantity, budget, and specific project requirements. It’s important to consider these factors and consult with both screen printing and sublimation print professionals to determine the most suitable method for your specific needs.
Both sublimation and screen printing have their strengths and can provide excellent results when executed properly. Whether you prioritize vibrant color reproduction, design flexibility, cost-effectiveness, or eco-friendliness, understanding the differences between these printing methods will help you make an informed decision for your apparel or promotional printing projects.