Textile fabric finishes are vital since they are used to alter the characteristics of fabrics making the fabrics have an improved texture, performance, and durability. There are many different types of finishes, which are carried out during or after fabric production, in order to provide designated characteristics required for various uses. These functions where the textile finish can assist include softness and imparting water resistance, enhancing strength, flame resistance, and so on, make textiles versatile in meeting functional and aesthetic demands. In this blog, there are going to be explained types of textile fabric finishes, their uses and possible effects to the end product.
Introduction to Textile Fabric Finishes
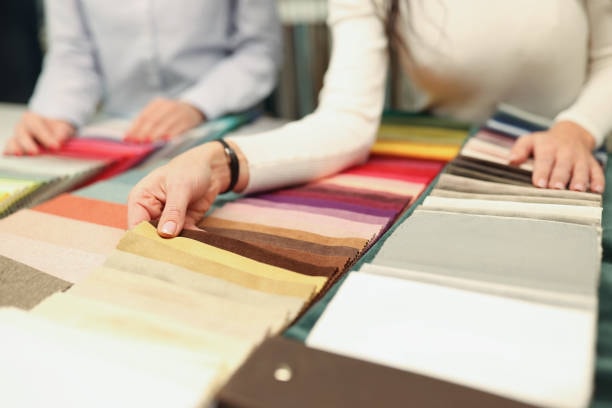
Textile fabric finishes are additionally treatments in textile involving chemicals or mechanisms used on fabrics to improve on their attributes. Such finishes change the feel, look and use of the fabric which suited it to particular functions or tasks. The fabric finishing process can be divided into two main categories: The divisions are mechanical finishes and chemical finishes.
Mechanical Finishes

Mechanical treatments can be described as finishes provided by altering the construction of the fabric materials. These mechanical finishing list involves brushing, calendaring, and embossing among others, which add value to the texture of the fabric and its outlook.
Chemical Finishes
Chemical finishes are those in which the fabric is treated with some chemical with an objective of providing raw fabric with some specific properties. Such finishes are Water Repellent Finish, Flame Retardant Finish, and Antimicrobial Finishes, which are applied to the fabric for improving the fabric’s performance and life span.
Types of Textile Fabric Finishes
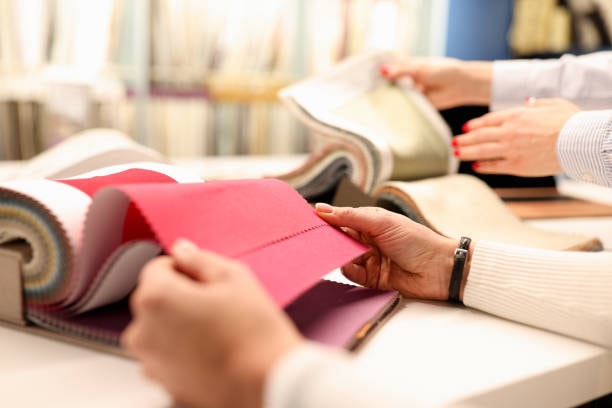
Textile fabric finishes are classified in many categories, where each category has been formulated for a purpose of providing certain characteristics to the fabric. In the next sections, this paper discusses the most frequently used and effective finishes in the various textile finishing field.
Softening Finishes
This categories of finishes are put on fabrics to give them a softer handle to the skin or to make them gentler on the skin. These finishes have very great demands and get applied on readymade garments along with home textiles.
Silicone Softeners
Silicone softeners are popular for softening the texture of fabric making cloths silky smooth to the touch. They create a thin continuous and flexible film on the surface of the fabric thus making is less abrasive and smoother.
Fabric Softeners
LA conditioner are normally used in washing which condition the clothes by depositing on the surface of the fabrics a thin layer of film which has a lubricating effect and eliminates static electricity.
Water Repellent Finishes
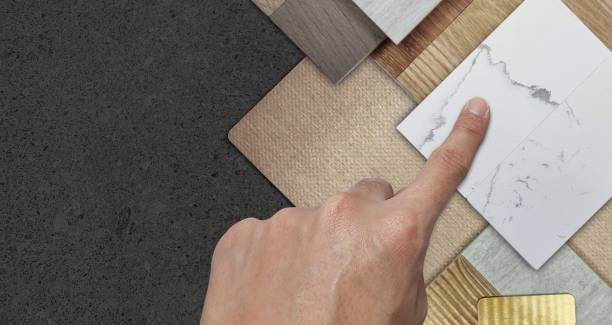
Water repellent finishes helps make synthetic fabrics final products to be unable to penetrate through water while at the same time it is breathable. Undoubtedly, these finishes are expected in outdoor and performance textile products.
Durable Water Repellent (DWR)
DWR finishes provide a water-resistant layer on the outermost layer of the fabric making it so that water forms droplets and runs off the fabric surface. This finish is popular in fashions woven fabrics that are made to be worn in cold and moist conditions, sporting wears, equipment and accessories.
Fluorocarbon Finishes
Fluorocarbon finishes make the fabric water and stain proof in that they do not allow any liquid to settle on the fabrics surface. It forms a physical shield that stops water and oil soluble stains from getting into the fabric.
Flame Retardant Finishes
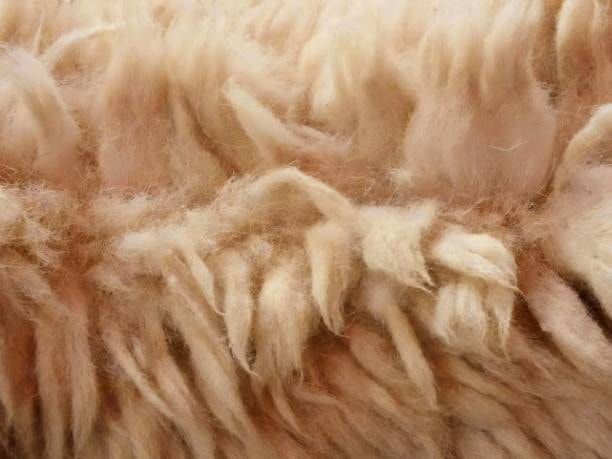
Flame retardant finishes are useful in fabrics which are used in the production of safety apparels, home upholsteries and places which are accessible by the public. These finishes also restrict the flame spread causing low casualties and losses in cases of fire outbreaks.
Phosphorus-based Finishes
Phosphorus-based finishes function in the method of char development and diminution of flammability. They are usually incorporated in garments that are worn by workers handling chemicals; in car interiors, among others.
Halogenated Finishes
Halogenated finishes burn by releasing halogen atoms that interrupt the burning process in a patient material. These finishes are rather useful but have provoked discussions in relation to the environment and human health.
Antimicrobial Finishes
Antimicrobial finishes prevent the breakout of bacteria, fungi and other microorganisms on the surface of the fabric. These finishes are useful in the medical textiles, sports wear and home textiles.
Silver-based Finishes
Silver-based finishes embark silver ions, in environmental interfaces, that hinder the growth of the microorganisms due to interference of their membranes. Such finishes are utilized often in physicians and activewear fabrics.
Quaternary Ammonium Compounds
It is biocidal and kills gram positive and negative bacteria, fungi, yeast, viruses and spores apart from being useful for sanitizing and disinfection of surfaces. They are often applied in hospital fabrics and personal sanitary items and articles.
Wrinkle-resistant Finishes
Wrinkle resistant finishes otherwise known as a semi durable finish or press finishes are treatments that hinder fabric from wrinkling and creasing. These finishes are commonly used in the garments particularly in the business and casual clothing.
Resin Finishes
Resin finishes interlink the fibers and make it smooth and wrinkle free in appearance. Still, they influence the softness and other properties, for example, breathability of the fabric.
Silicone-based Finishes
But the beauty of having applied silicone-based finishes is that the fabric is indeed wrinkle resistant withoutCogh any alteration on the hand feel of the fabric. The ordinary ones are preferred especially for their moderate performance.
Moisture Management Finishes
Moisture management finishes further improve the fabric’s gammons in relation to its capacity to pull moisture away from the skin and keep the wearer dry. These finishes are essential in sportswear and activewear products as these are used when performing sports activities.
Hydrophilic Finishes
The above finishes make the fabric to absorb moisture, and distribute it over the surface area of the entire fabric, in a way that makes evaporation to occur. It is often found in its application in performance textiles.
Hydrophobic Finishes
Water resistant coatings do not let water to get through to the fabric in the first place, this is because they are water repellent. These finishes are normally applied alongside hydrophilic finishes since they help control the amount of moisture that is absorbed.
UV Protection Finishes
UV protection finishes prevent or reflect damaging ultraviolet (UV) rays thereby preventing skin burn and therefore decreasing the rate of skin cancer. These are the finishes that are useful for apparels that are worn over the exterior human body, and accessories such as caps, belts, wallets, hand bags, shoes etcetera.
Titanium Dioxide Finishes
Titanium dioxide finishes work to block the UV radiation so that it is not transferred to the skin. They are widely applied in summer clothes and beach accessories.
Zinc Oxide Finishes
Coated fabrics offer UV protection since such finishes emit and also take in the rays of the sun. They are commonly employed in application with fabrics that provide protection from the uv-sun rays.
Anti-static Finishes
Anti-static finishes are used to avoid accumulation of static electrical charges on the fabrics’ surface thus rejects static cling and enhances comfort. These finishes are significant in wearing apparel particularly in the heat setting the dry areas.
Conductive Finishes
Conductive finishes use carbon or metallic fibers to ground out static charges; miles of carbon or metallic fibers are used. It is applied in technical textiles and workwear.
Moisture-absorbing Finishes
Reducing static electricity is achieved through moisture-absorbing finishes as they raise the fabric’s moisture level. They are applied in the daily wear clothes most of the time.
Applications of Textile Fabric Finishes
Textile fabric finishes are used in many products, to improve their functionality and open up new uses. In the following passage, various configurations of these finishes in different industries are discussed.
Apparel and Fashion
Fabric finishes in the apparel and fashion industry are used to beautify the fabric, make it comfortable to wear and at the same time very functional. Functional finishes make items softer to the touch, and make them less prone to wrinkling. The last sustainable components of clothing are moisture management finishes as it is important for sportswear that an athlete or a sportswoman does not sweat during his or her sporting activity. UV protection finishes are used for design of outdoor wears while the antimicrobial finishes help to maintain the garment fresh and smell free.
Home Textiles
Thus, the types of fabric finishes that improve its functioning and longevity are hugely beneficial to home textiles. To eliminate cases of what new upholstery and curtains being stained by water, water repellent finishes are used. Flame retardant finishes are therefore a vital necessity especially when it comes to home furniture. Laundry techniques involve the use of antimicrobial finishes for the bed linens and the towels to enhance on hygiene and freshness. Resistant finishes make table cloths and bed sheets not to develop wrinkles and hence they maintain their business like appearance.
Outdoor and Performance textiles
Textiles for outdoor and performance can only be used after appending some special treatments that can enable them to endure the tough weather and tough usage. The same way that water repellent finishes reduce the soaking of outer wears and gears in rainy or wet seasons. UV protection finishes guard the skin against the effects of UV rays specifically during sporting activities. The end fabrications are also a sign that moisture is managed to provide comfort in the course of the physical activities. Here, it is crucial to introduce antimicrobial finishes to replenish the sanitization factor in the outerwear and performance wear designs.
Medical Textiles
Contemplation of finishes for medical textiles shows how these textiles are dressed for promoting cleanliness, safety, and comfort. Sanitizing finishes, avoid growth of pathogenic bacteria on the medical textiles and hence minimize chances of infections. Flame retardant finishes are applicable in medical facilities for safety. Moisture management finishes reduce the instances of patients feeling wet at different parts of their body. Anti-static finishes are also important in the OR rooms and in other special areas temporary finish.
Industrial Textiles
Textiles for use in industry call for treatments that raise the fabric’s strength and longevity. App-based flame retardant finishes are commonly used in protective clothing used in hazardous areas. Shielding from moisture and chemical’s industrial cotton fabrics are treated with water repellent finishes mechanical finish. Anti-static coating limited the build up of static in the technical textiles. finishes created make the industrial fabrics more crease resistant so that they do not lose either the form or the appearance they are assigned.
The Impact of Textile Fabric Finishes on Sustainability
On the same note, the textile fabric finishes provides a lot of benefits but it also has drawbacks, most especially when it comes to environmental sustainability. Some of these finishes contain toxic ingredients or are produced with the help of dangerous chemicals, and their creation is accompanied by enormous water and energy consumption. In order to overcome these problems, textile industry has started using sustainable and environment friendly processes of fabric finishing processes.
Eco-friendly Finishes
Green is used in their finishes to ensure products have less or no effects on the environment and can support sustenance. These finishes fumigate using bio-degradable and toxic chemicals whereby limiting pollution and negative impacts on ecosystems. For instance, water borne coatings do not use hazardous solvents and cut back water consumption.
Sustainable Manufacturing Practices
Eco-friendly production processes focus on minimizing the negative impact of cotton textiles’ manufacture. Such processes as digital printing and plasma treatment are used to minimize the usage of water and chemicals. Energy efficient operation of processes and utilization of renewable resources of energy adds to the overall sustainability.
Recycled and Renewable Materials
Sustainable resources such as recycled and renewable are going mainstream when it comes to textile material production. Some strategies are the utilization of recycled fibers and biodegradable finishes because they prevent wastage of resources in the textile chain. Organic finishes derived from plants provide a green solution that is friendly to the environment.
Innovations in Textile Fabric Finishes
Indeed, with the technological progress the development of new and more effective, finishing processes of fabrics performances more enhanced than having negative impacts on the environment. In this part, we provide some of the most current advancements in textile fabric finishes.
Challenges and Future Directions for textile fabric finishing
Though, textile fabric finishes have advantages, they also have some difficulties, which should be solved for both safe and effective application. Here some of the main issues and the prospects for development of the textile fabric finishes are described.
Negative influence on the Environment and Human health
A stitch can be as hazardous as the chemical finish where some of the finishes are health conscious and environmentally unfriendly. The type of finish to be avoided includes the fluorocarbons because they are known to remain in the ecosystem and even build up within species. Due to these worries, the industry is shifting towards the evolution and utilization of new safer forms of remedies.
Regulatory Compliance
Laws that pertain the usage of chemicals in textiles products are also being enhanced from time to time. Manufacturers must make sure that their finishes are following the legislation as the REACH and the ZDHC program. Pursuant to such regulations is mandatory for providing safety and sustainability of the textile product.
Demand Awareness & Consumer
The people are getting more conscious about the environment and are looking for products that are friendly to the environment, including the textiles. As for the consumers, there is a gradual change of perception leading to the more frequent use of innovative fabric finishes. To meet these demands the manufacturers must conform by doing rigorous research in developing finishes to match the consumers expectations in both performance and sustainability.
Conclusion
Adhesive finishes in textile fabrics can be used as end-use finishes to improve the feel as well as performance characteristics of textile fabrics. These finishes include softening and water repelling abilities, flame resistance, and antibacterial characteristics that are fitting for many uses. Nevertheless, the manufacturing process both of creating fabric finishes and its utilization leads to environmental and health issues but the industry is advancing progressively towards green solutions. New possibilities included in nanotechnology, bio-based finishes, smart functions, and plasma treatments constitute the potential future directions of the PF of textile fabrics.
Thus, it is obvious that the consumer awareness of sustainable products and increased demand compel the textile industry to address the development of the sophisticated, multifunctional semi durable, and sustainable finishes. This way the industry can design fabrics that not only provide the necessary performance, but also enter the world as eco friendly products as supported by green chemistry, smart technologies, circular economy and collaboration.
Thus, the detailed analysis of the textile fabric finish as a promise exhibition shows the opportunities of improving the fabric characteristics and discovering new uses for fabrics. Hence, through knowing the types, uses and even breakthrough of fabric finishes, one is able to gain insight of the complex procedures final process that is put in place in tackling the importance of fabric finishes in enhancing the textiles in oururnal lives. Thus, it can be concluded that the emphasis on sustainability and development in the future will remain further advances textile finishes to enhance the sustainability of the textile industry.