From a factory specializing in OEM production for Shein and Kuaiyu, it has now become a high-end quality production factory. We mainly did the following:
1. Improved the work quality of production workers.
2. Improved the working environment.
3. Adapt a unique quality management process.
Improved the work quality of production workers
Shein and FASTFISH(fast fashion brands in China) have very large orders. In 2017, we produced about 10,000 pieces of clothes for these two brands per day. There were 150 workers in our factory at that time. Moreover, the production volume increased even more, so, the factory must rent larger workshops and warehouses, which has increased our operating costs. Labor costs and factory rents are getting higher and higher, so the potential risks of factory operations become greater. However, the profit of these orders is not very high. The quality of these clothes is also not high, which easily leads to the low quality concept of the workers in our factory.

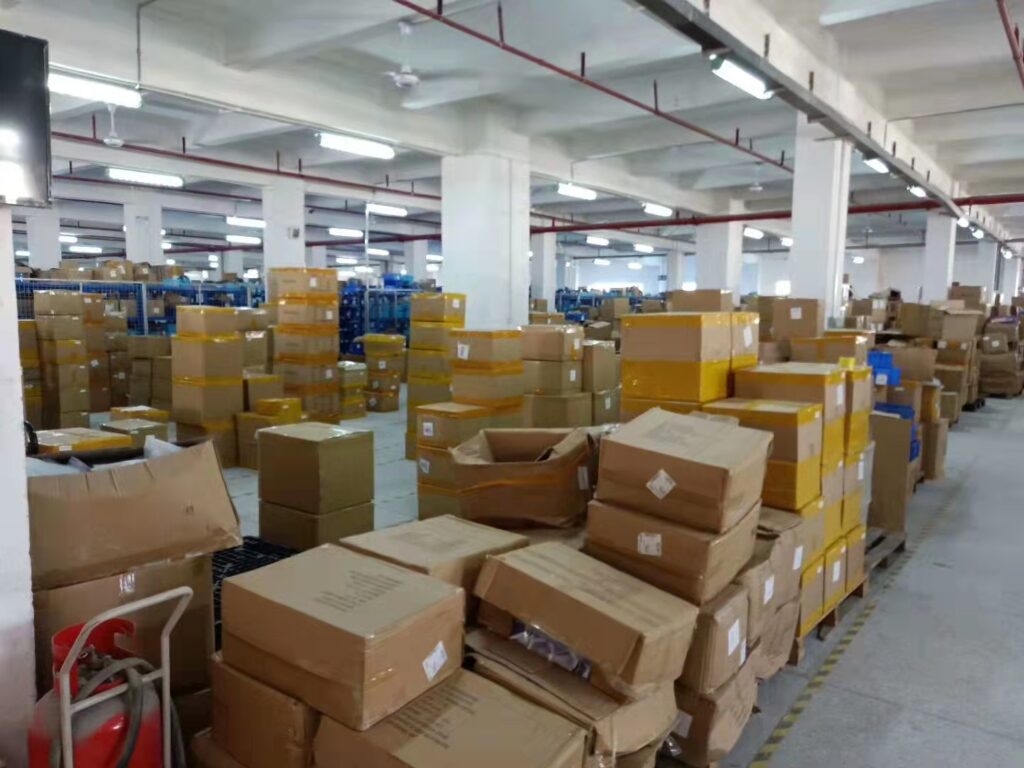
Therefore, I decided to allow my factory to move towards high-end quality. I started to reduce the accepted number of orders for the Shein and FASTFISH brands, and switched to producing clothes for the 3 known brands in Guangzhou Baima Market. Our own Tmall brand, Ajiduo has also begun to develop in the direction of high-end clothing. In doing so, most of our workers have resigned because it is difficult to adapt to such quality requirements. My factory has shrunk from 150 employees to 30. But now, it has more than 60 employees and is growing. For this quality reform, we almost replaced 90% of our employees. The process was very painful, but I think I was right.
There is actually no secret in making high-quality clothes. We just need to let our employees be patient with each piece of clothing. Yes, be patient. It’s that simple.
Improved the working environment
The working environment in most garment factories in China is not very good because garment production is inherently a low-profit business. We cannot rent a factory in a beautiful office building.
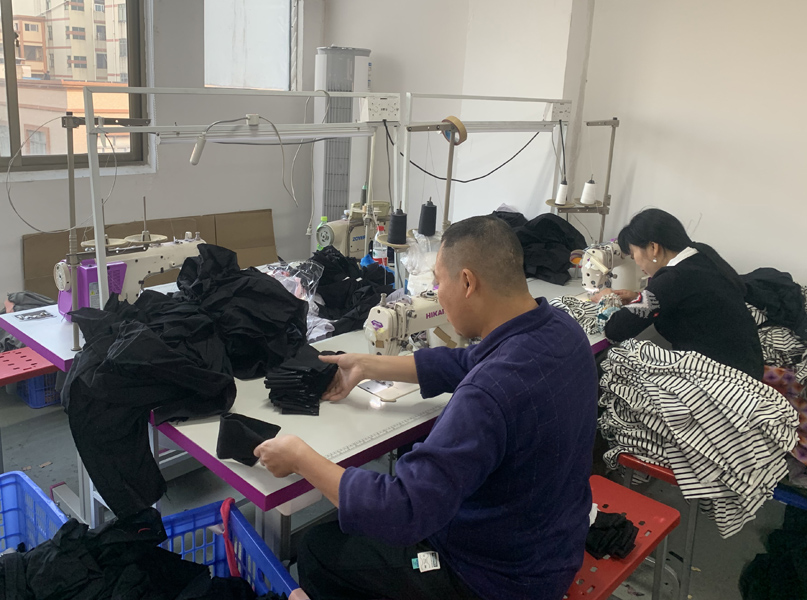
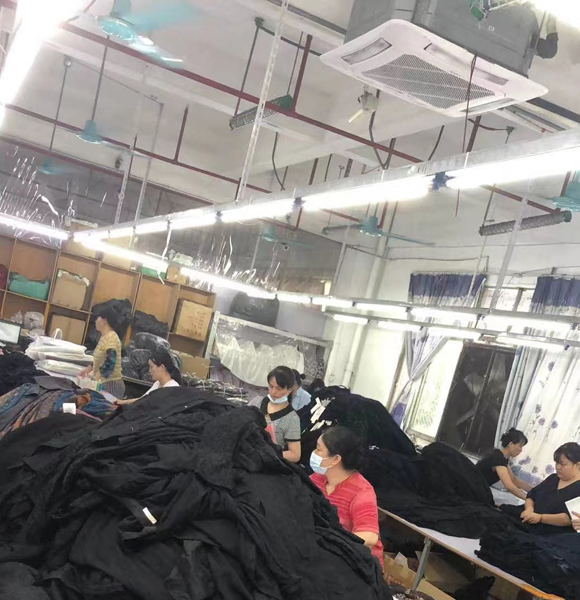
Because the number of people in the factory has decreased, I moved from a 3,000-square-meter factory to a 1,000-square-meter factory, which saved me some operating costs. I used the money I saved to install air-conditioning in the factory and improve the diet of the workers. Now, our factory is the only one in our industrial zone with air-conditioning in the workshop, and our diet is also the best (2 meats per meal, 2 vegetarian dishes, 1 soup).
The improvement of the office environment results in an increase in the productivity of workers, and the happiness index of workers working here has also increased.
Adapted a unique quality management process
Our quality management is divided into 4 processes:
1. When the clothes are still semi-finished products, Quality Inspector A will start random inspections. If there are problems with the production of 5-10 pieces of clothes, they must stop production and conduct a comprehensive investigation.
2. When all the clothes are produced, Quality Inspector B will inspect each piece of clothing. If there are clothes with quality problems, the production team must repair them immediately.
3. When the clothes are ready to be packed and shipped, the Quality Inspection Supervisor randomly selects 5% of the quantity for inspection. If there’s even just 5 problems found, the entire batch needs to be re-inspected.
Moreover, we have to clean up the thread in every process to ensure that every piece of clothing has no flaws in the hands of customers.
Start from the boss
Whether a factory is going to run well or not, the boss’s ideas are very important.
In 2018, I joined a charity training organization together with the other 30 people. My new friends and I have used some games and activities to unite us all. We worked as a team. After 6 months of hard work, we finally achieved our ultimate goal. We were able to raise donations on the street together. Then, we decided to donate some of the money to build an Elementary School Building to a poor township in Yichun County, China.
This incident taught me to treat society better, to be responsible for work, and to be serious about everything. Although there are only 60 people in our factory now, we are working as a team. I must let them have better work goals for them to be able to get a better life.
As for my customers, no matter how large or small the customer’s order quantity is, I always require my staff to make every piece of clothing perfect when it is delivered to the customer.
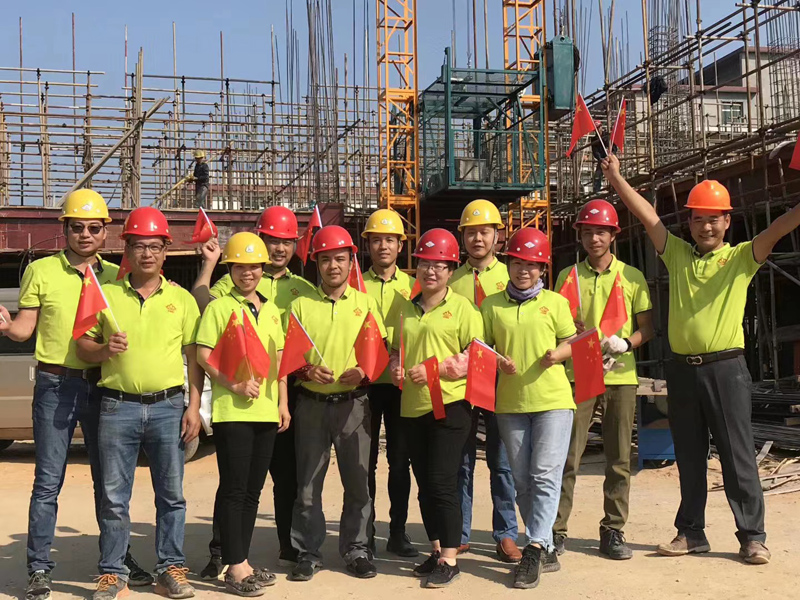

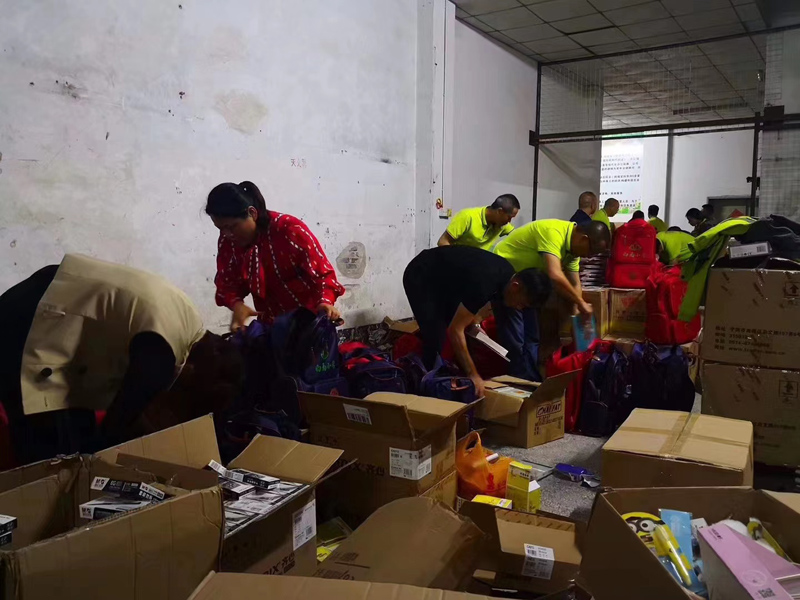
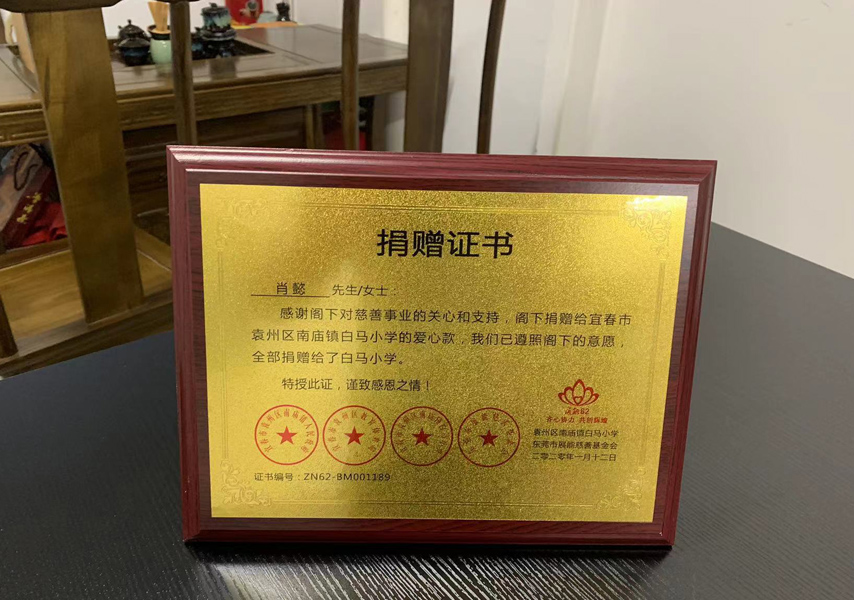